Summary of common failures of mask machine equipment during commissioning
Summary of common failures of mask machine equipment during commissioningWhat should I do if there is a problem during the commissioning of the mask machine? Help everyone solve this problem today. The faults that will appear during the debugging process or the use of the mask machine equipment are listed, and the reasons are analyzed, and the solutions are given, hoping to help everyone.
Summary of common failures of mask machine equipment during commissioning
Fault 1. Uneven welding and distortion of the workpiece.
Solution: 1. Check whether the size of the workpiece is different.
2. Check whether the operating conditions cause deformation of the work.
3. Adjust the buffer speed or pressure.
Fault two, the base support is not stable.
Solutions: 1. Improve the support points where necessary.
2. The base is redesigned.
3. Change to a hard base.
4. If a large area of bakelite is inclined, it needs to be reinforced.
Failure 3: The contact surface of the welding head, base and workpiece is not flat.
Solution: 1. Redesign the guard point to make the height uniform.
2. Adjust the horizontal screw.
3. Check whether the prerequisites are true.
4. Check the shape and size of the workpiece.
5. The side is bent, and the workpiece is added with ribs.
6. Modify the metallurgy tool to avoid the workpiece bending outwards.
Fault 4. The workpiece error is too large.
Solution: 1. Tighten the tolerance of the workpiece.
2. Re-modify the workpiece size.
3. Check the operating conditions (pressure, delay timing, welding timing, curing timing, etc.).
Fault 5. Improper splicing work piece misalignment.
Solution: 1. Check whether the workpiece is offset when welding.
2. When checking the combination, whether the workpiece is aligned.
3. Check the parallelism of the welding head, workpiece and metallurgy tool.
Fault 6. Lack of close contact on the joint surface.
Solution: 1. Check the workpiece size.
2. Check the tolerance of the workpiece.
3. Check the position of the thimble on the joint surface.
4. Check the alignment of the workpiece combination.
5. Check whether the workpiece is sunken.
6. Check the fit between the workpiece and the welding head.
7. Check whether the support of metallurgical tools is appropriate.
Fault 7. The ultrasonic welding results are inconsistent
(1) The proportion of additives is too high
Solution: 1. Reduce the filling.
2. Check the operating conditions.
3. Change the type of filler, that is, change the short-line cone into a long-line cone.
(2) Uneven distribution of additives
Solution: 1. Check the operating conditions
2. Check the mold design
(3) Poor material quality
Check operating conditions
(4) Poor fit of workpiece
Solution: 1. Check the workpiece size.
2. Check the workpiece tolerance.
3. Check the operating conditions
Fault 8. Turn on the main power switch, the fuse blows
1. Ultrasonic power board short circuit;
2. Short circuit of rectifier bridge;
3. The starting current has a great impact, and the fuse capacity is too small;
Fault 9, excessive ultrasonic welding
Cause analysis and solutions: 1. The dimensions of the work object after overmelting are different
2. Too much damage to the appearance of the work.
3. Adjust the lowest point fine adjustment screw;
4. Replace the welding head with lower amplitude.
5. The welding time is too long to be shortened.
Fault ten. Press the welding button, the welding head will drop, but it will not rise after welding.
Cause analysis and solutions: 1. Insufficient air pressure;
2. Defective solenoid valve;
3. Adjust the air pressure;
4. Maintenance program board;
5. The time adjustment switch is damaged;
Fault 11. The overload light is on during operation.
Reason analysis: 1. Loose welding head;
2. Improper frequency adjustment;
3. The welding head is broken;
4. Excessive pressure;
5. The machine power is too small.
Trouble 12: The power indicator is off, the fan of the vibration box is weak, and it cannot be shaken or the welding strength is weak.
Reason analysis: 1. Low power supply voltage;
2. The input transformer is damaged;
3. Poor contact of the power socket.
Trouble 13: Press the welding button, the welding head will immediately fall and touch the workpiece to rise without vibration.
Reason analysis: 1. The downstroke has not reached the welding position;
2. Poor contact of the travel switch;
3. Bad pressure trigger system.
Fault 14. The impact of the welding head rising or falling is too large.
Reason analysis: 1. Improper buffer adjustment;
2. Buffer adjustment locks up;
3. The descent speed is set too high;
4. Poor cylinder cushioning.
Fault 15, air pressure, power supply, welding head are normal but unable to start.
Reason analysis: 1. Poor contact of emergency ascent button;
2. Defective program control circuit;
3. The start button is damaged;
4. The solenoid valve is damaged.
Fault 16. The input energy is too little.
Reason analysis and solutions: 1. Increase the use pressure;
2. Increase the welding time;
3. Increase the amplitude;
4. Use models with higher power;
5. Poor resonance of ultrasonic welding head.
Fault 17. Excessive input energy.
Reason analysis and solutions: 1. Reduce the use pressure;
2. Reduce welding time;
3. Reduce the number of amplitude segments;
4. Slow down the descending speed of the welding head;
5. Insufficient welding.
Breakdown 18. Use materials with poor fusion properties.
(1) Use secondary materials
1. Check the materials with the factory.
2. Check the operating conditions.
(2) Surface damage: the temperature of the welding head rises
1. Check whether the welding head screws are loose.
2. Check whether the welding head tool is loose.
3. Shorten the welding time.
4. Cooling the welding head.
5. Examine the interface between the welding head and the transmission.
6. Check whether the welding head is broken.
7. If the welding head is titanium, change to aluminum.
8. If the welding head is copper, reduce the magnification.
(3) Partial bruising of the workpiece
1. Check the workpiece size.
2. Check the fit between the workpiece and the welding head.
(4) Improper fitting of workpieces and metallurgical tools.
1. Check if the support is proper.
2. Redesign the metallurgical tools.
3. Inspect the changes of mold and mold door workpiece.
(5) Surface damage: alumina (from welding head).
1. The welding head is treated with hard chrome.
2. Use anti-thermoplastic film mold (bag).
(6) Surface damage: improper bonding of welding head and workpiece.
1. Check the workpiece size.
2. Redo the new welding head.
3. Examine the changes between the mold and the workpiece.
Fault 19. The current is too large and overloaded (over 7A) during welding.
Reason analysis: 1. The air pressure is too high;
2. The output gear is too large, and the impact current is large;
3. The buffer is too small;
4. High trigger pressure and long delay time.
Fault 20. Without ultrasonic output, ultrasonic welding is impossible.
Reason analysis: 1. The ultrasonic crystal plate is broken;
2. The ultrasonic vibration board is broken;
3. Welding overload protection;
4. The output circuit fuse is broken.
5. The gear switch is at 0 or the contact is not good;
6. The output line is not well connected or short-circuited.
Fault 21. The size of the joint surface is uneven.
Solution: 1. Redesign the joint surface.
2. Check the operating conditions.
(1) The workpiece is too tight
1. Relax the fit of the workpiece.
2. Relax the tolerance of the workpiece.
(2) The workpieces cannot be aligned after welding, and the workpieces are not aligned when assembled.
Solution: 1. Add piles between the two pieces.
2. If possible, design tools to guide.
(3) Improper support of the base
Solutions: 1. Redesign the appropriate supporting tool to elevate the base where necessary.
2. If the bakelite is inclined, add a hard bracket.
(4) Side wall bending
Solution: 1. Add ribs to the side wall of the workpiece.
2. If the bakelite is inclined, add a hard bracket.
(5) The tolerance of the workpiece is too large
Solution: 1. Tighten the workpiece tolerance.
2. Check the operating conditions.
(6) During welding, internal parts are damaged and the welding time is too long.
Solution: 1. Increase the amplitude or pressure to reduce the damage of welding time.
2. Adjust the buffer speed and delay time.
Fault 22. The welding time is too long.
Solutions: 1. Increase pressure or amplitude to reduce welding time.
2. Adjust the buffer pressure.
(1) The contact surface of the welding head, workpiece and base is poorly fitted.
Solution: 1. Check the parallelism between the welding head workpiece and the base.
2. Check the fit between the welding head and the workpiece.
3. Check the fit between the workpiece and the base.
4. Plinth the base where necessary.
(2) The influence of workpiece deformation is too great.
Solution: 1. Reduce the influence of deformation.
(3) The welding time is too long
Solution: 1. Reduce welding time.
(4) The workpiece absorbs too much energy
Solution: Reduce the amplitude.
1. Lock the welding head;
2. Press the sonic inspection button and adjust the sonic adjustment screw to minimize the current indication;
3. Change the mold;
4. Replace related parts;
5. Overhaul the power tube;
6. Repair the power amplifier circuit.
If you want to know more about it please do not hesitate to
contact me. WhatsApp:+86-15966835076.
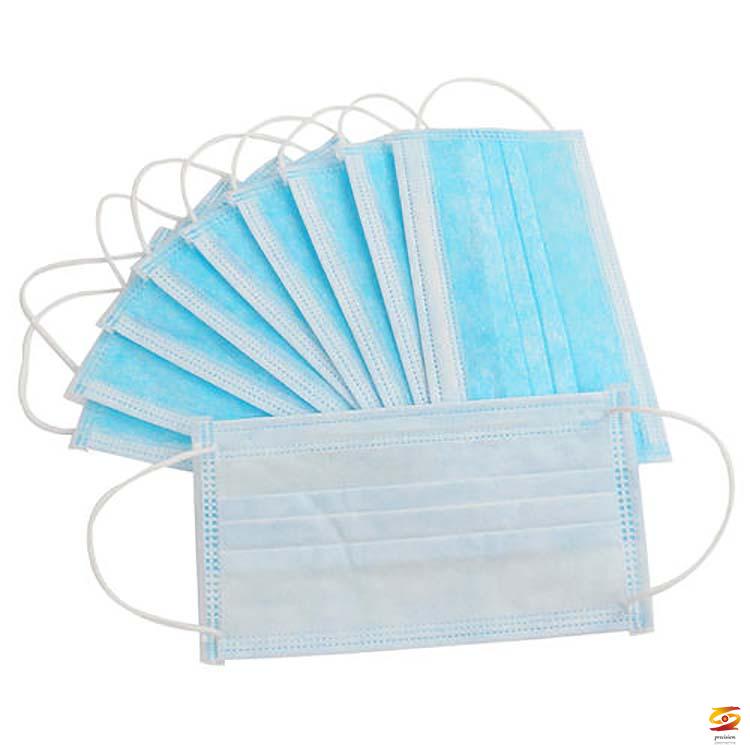
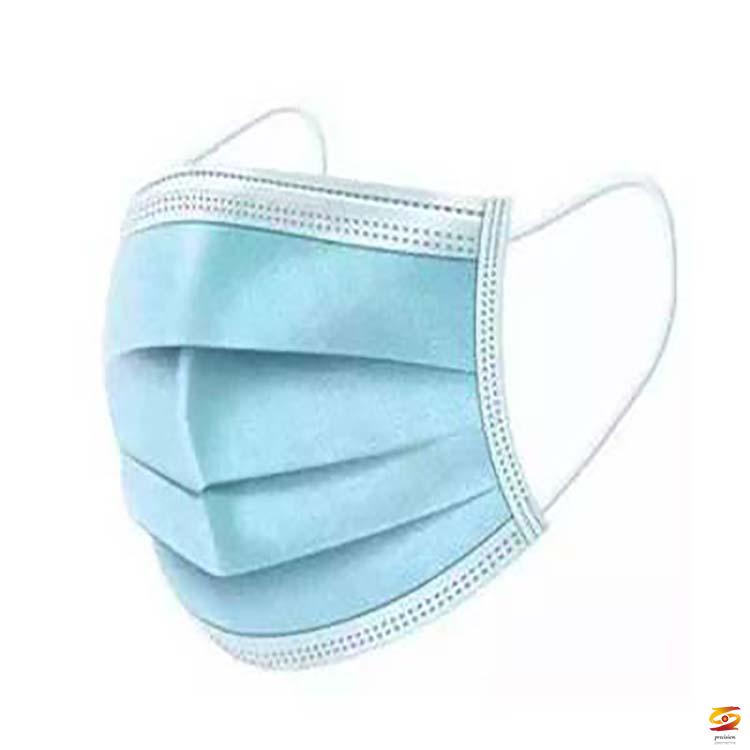
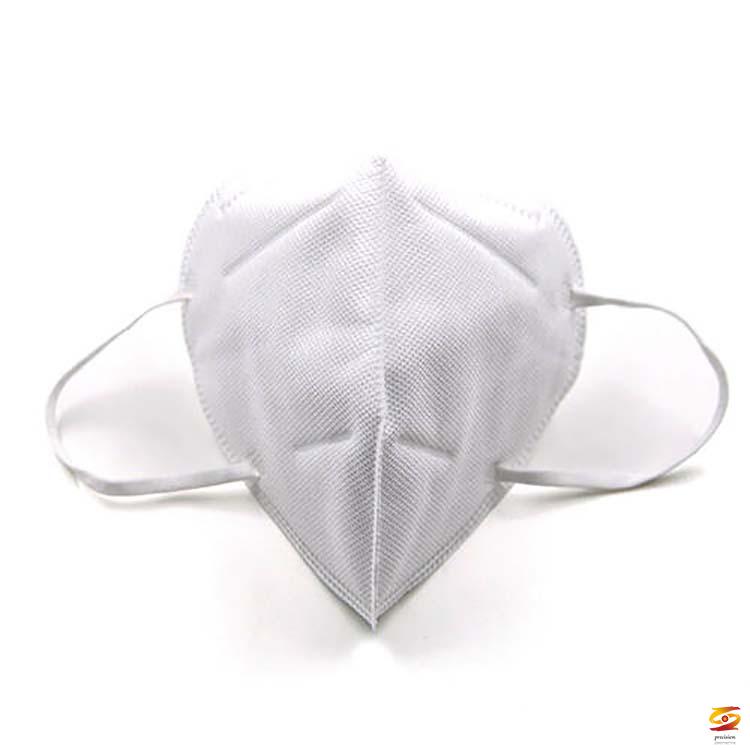
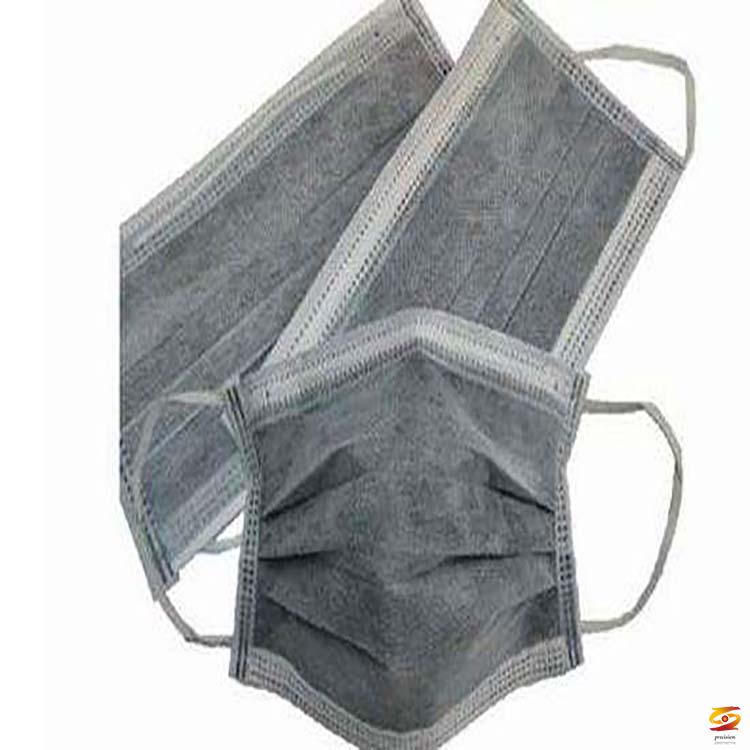