Common problems and solutions of melt blown cloth extrusion
The design principle and structure of the meltblown machine equipment is not complicated, but the maturity of all equipment must go from raw to mature, and experts also come from rookies. Although many equipment manufacturers used to make plastic machines, they have never made meltblown machines. So the equipment you bought is actually the first product of others. To put it bluntly, the 650 and 800 most people buy at present are small earth cannons, and the machines above 1600 are better. The difference between a good machine and a good one is not in function, but in details, but in factory experience and production experience!The melt-blown nonwoven process is actually very simple. The polymer melt extruded by the screw extruder is sprayed with high-speed hot air to make the fine flow of the melt extremely stretched to form ultra-fine fibers. These ultra-fine fibers coagulate A web is formed on the screen or roller, and becomes a nonwoven fabric by self-adhesion.
The technological process is as follows: polymer feeding→melt extrusion→fiber formation→fiber cooling→web forming→adhesive reinforcement→trimming and winding→finished product.
From the point of view of the manufacturing principle of the cloth: the melt-blown method is to form ultra-fine fibers, let these ultra-fine fibers condense on the screen or roller to form a web, and rely on their own bonding to become a non-woven fabric. In order to easily form ultra-fine fibers, PP materials with ultra-high fluidity are required. When other factors remain unchanged. The higher the melt, the finer the filaments, and the easier it is to spray products with a higher filtration level. The higher the melt, the better the better the better cloth.
At present, there are many polypropylene modified materials. At present, regardless of the size of the modified factory, the PP material melt is marked as 1500. But this is only one of the indicators. The flexibility and processing versatility of the material are in the index. No. And you can only try it yourself. Many manufacturers don't know the adjustment data required by their melt-blown materials on different machines.
If you want to know more about it please do not hesitate to
contact me. WhatsApp:+86-15966835076.
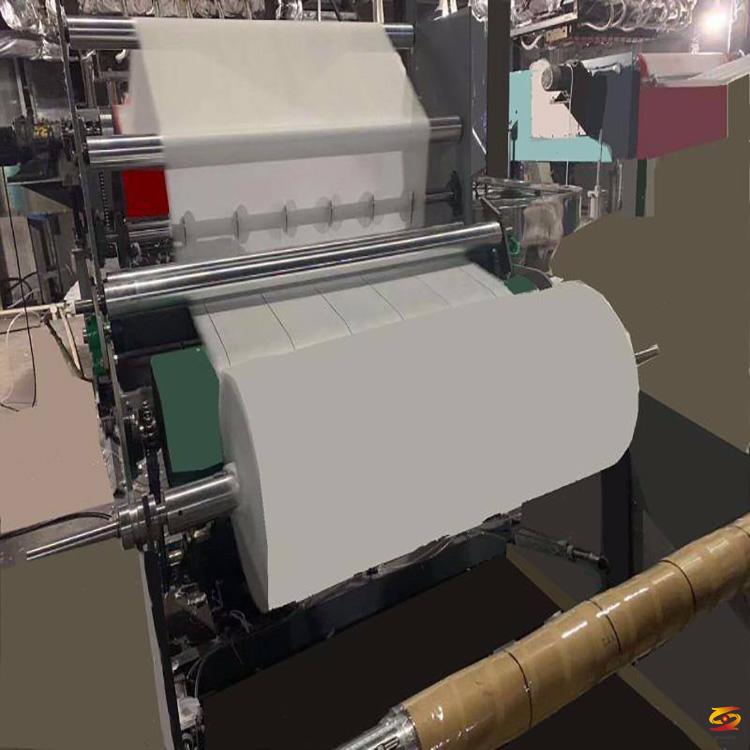
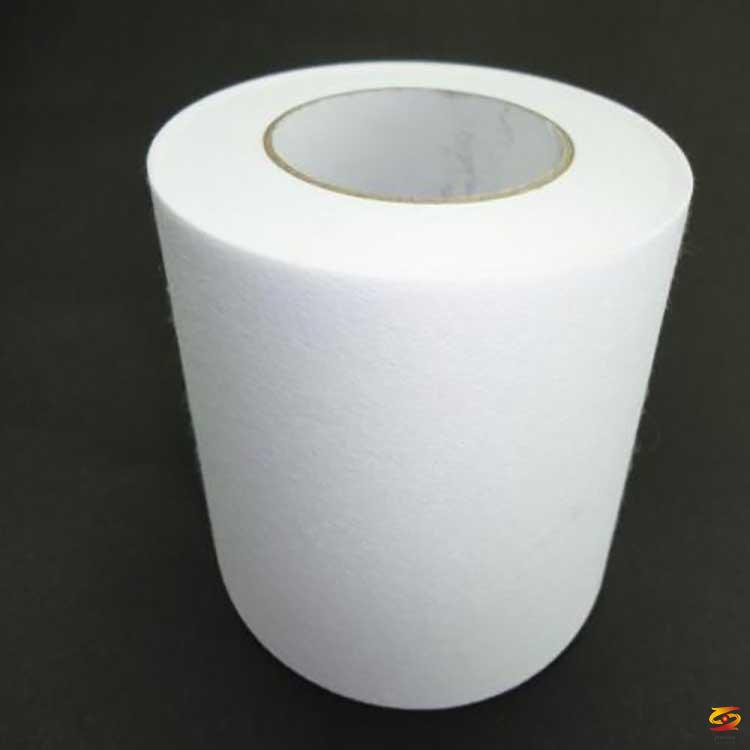
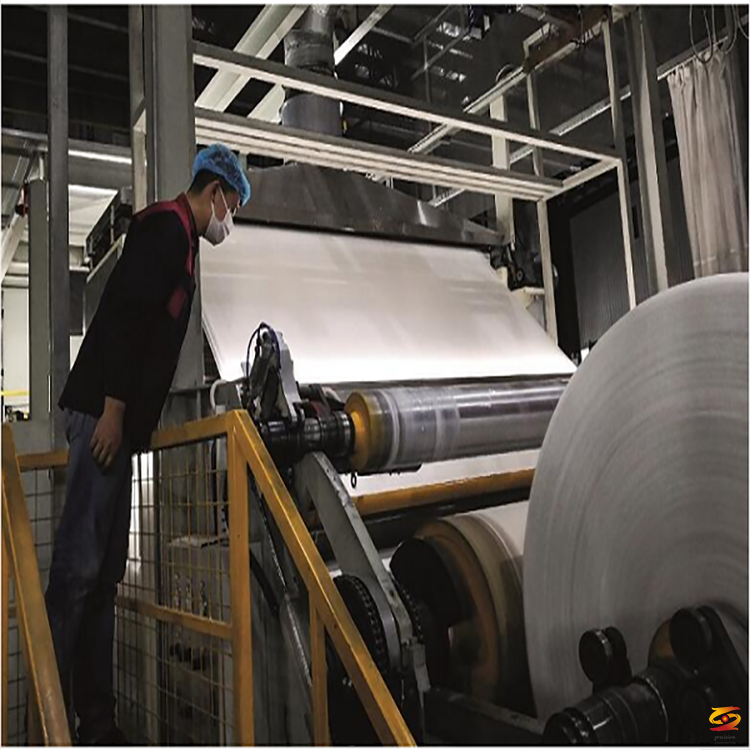
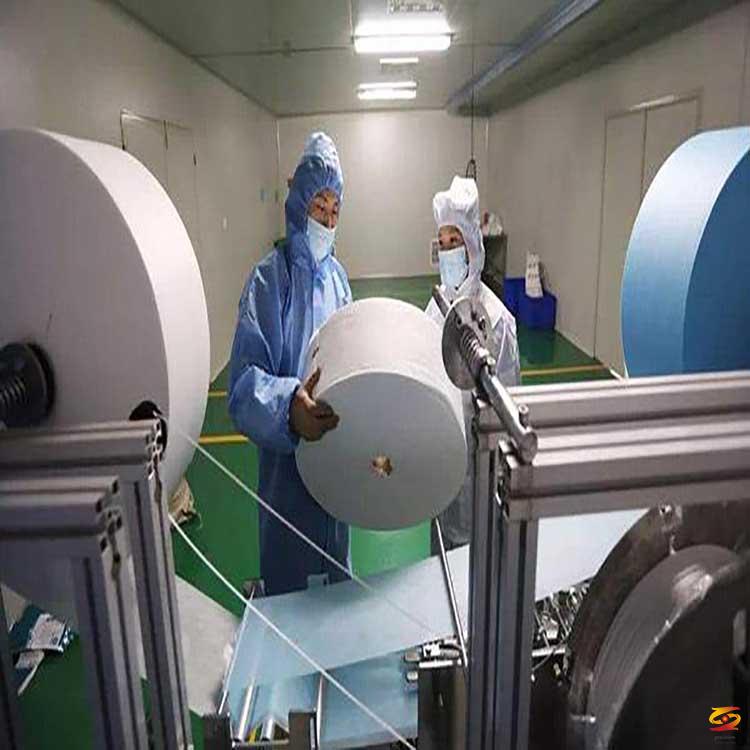
First, the customer encountered common problems in the process of solving the problem:
1. The same material starts to work, and the cloth will not spray out in a few days
Some materials have a low melt quality after being placed for a few days. Many products have seen that the melt quality is about 1500 before leaving the factory, and it will be 1000 after a few days at the customer's factory. This will cause the starting material to be used well. There is no cloth. Different melts require different processing temperatures. This is caused by the inadequate processing technology in the production of meltblown materials. The stability of the material is very important.
2. The toughness of the cloth is not good, easy to be brittle and easy to break
This is currently the most encountered problem. Considering the melt of the material alone is 1500, it is normal that the sprayed cloth is brittle and fragile. Therefore, in the production formula of melt-blown materials, relevant ingredients are needed, and different proportions are used to solve this problem. Moreover, some materials must be added in the production stage, and later added to the meltblown machine often encounters uneven processing, plugging and other problems. The problem of poor toughness is too common. Find me to help you. Compound formula, imported ingredients.
3. The sprayed cloth smells
The main reason may be that after the air compressor is used for a long time, the oil and gas filter fails, and oil mist is sprayed with the air flow. In short, the cloth has a smell. Although the cloth filtration level may be up to the standard, it has an odor and is harmful to the human body. It is recommended Replace Roots blower. There is also a problem with the ingredients used in the modification process, especially with initiators produced by some small factories.
4. Use non-melt spray material to spray melt-blown cloth
Many small factories start with non-melt spray materials to spray melt-blown cloth, such as SECCO 2040. This filtering level is not up to standard. And it cannot be used for medical products.
5. The melt-blown material of the big factory cannot spray a good cloth
To put it plainly, this is a mismatch between the material and the machine. In other words, your machine does not eat this material. After the material is produced and tested, the formula ratio will not be changed. It has its processing range, but your machine can easily find this processing range. Faced with this problem, either change the machine, or add ingredients during meltblowing, both of which have to be tested. The best thing is to resolutely change the dressing...
Second, it is very important to adjust the machine. No matter how good the machine is, it will not be adjusted well. The following are the aspects to be adjusted:
A. Receiving distance
The distance from the exit of the die nozzle spinneret to the receiving screen or roller is called the receiving distance of the melt-blowing process. When the receiving distance decreases, the fiber fineness decreases obviously; when it decreases to a certain level, the fineness decreases slowly; when the receiving distance is too small, the fiber fineness increases again. This is because the area where the melt-blown fiber is stretched and thinned under the action of hot air mainly occurs at a short distance from the spinneret hole. The fiber fineness has a significant effect on the tensile properties. The fiber is thin, the winding nodes are many, and the fiber is stressed Uniform, the strength increases, but after increasing to a certain extent, the tensile properties will tend to decline. The receiving distance also affects the bulkiness of the meltblown fiber web and the degree of adhesion between the fibers.
Under normal circumstances, the receiving distance is reduced, the cooling and diffusion of the hot air flow are insufficient, and the thermal bonding effect between the fibers is strong, resulting in a decrease in the bulkiness of the product, an increase in the fiber volume density, and a decrease in the product elongation. When the receiving distance increases, the bulkiness of the fiber increases, while the fiber fineness increases, the product porosity becomes larger, the filtration efficiency becomes worse, the resistance becomes smaller, and the product elongation also increases. When the receiving distance is too small, the fibers in the fiber web will be curled and agglomerated together, the product's bulkiness will decrease, affecting the suction efficiency of the bottom of the net, and the "flying flower" defects will occur; in severe cases, the fiber will not be completely cooled, causing ice wire.
B. Hot air speed and hot air temperature
Under the same process conditions, the hot air speed increases, the fiber fineness will become smaller. This is because the hot air velocity increases, and the fiber drafting force to the spinneret hole increases, so the fiber fineness becomes smaller; but when the air pressure reaches a certain value, the decrease in fiber fineness will gradually slow down and the fiber fineness The CV value decreases accordingly. This is because the hot air flow rate per unit time increases, the tensile force acting on the fiber increases, and the tensile effect on the fiber is sufficient. Therefore, all fiber deniers are decreasing, and the fineness CV value will naturally decrease.
The performance on the melt-blown nonwoven fabric is that the feel changes from hard to soft, the fiber entanglement increases, and the thermal bonding effect increases, the fabric surface changes from rough to dense and smooth, and the tensile breaking strength increases, but the tensile The elongation at break will decrease because the slip path of the fiber node becomes larger; when the hot air speed is too large, the "flying flower" defect will appear, and the tensile breaking strength will also decrease. Under the same process conditions, as the hot air temperature increases, the fiber fineness will become smaller, and the fineness CV value will also decrease; when the hot air temperature increases to a certain range, the fiber fineness changes slowly, while the fineness CV value Significantly lower; when the temperature continues to increase, the fiber fineness will become significantly smaller.
This is due to the fact that hot air drafts the fiber during spinning. The temperature increase can delay the cooling and solidification of the fiber, the drafting effect is enhanced, the fiber fineness and CV value are reduced, and the tensile strength of the melt-blown material is increased. The tensile elongation at break decreases. Decreasing the hot air speed or hot air temperature will increase the melt blown fiber fineness, and the porosity will also increase, the resistance will become smaller, and the filtration efficiency will become worse; increasing the hot air speed or hot air temperature, the melt blown fiber fineness will decrease, and the porosity will also increase. The reduction will improve the capturing capacity of the fiber web, the filtration efficiency will increase, but the filtration resistance will become smaller.
C. Working area temperature
Temperature is one of the important parameters of polymer processing technology and has an important influence on the rheological behavior of polymers [7]. Wang Yanfei and others pointed out that when the melt is extruded from the spinneret, due to its own viscoelasticity, the extrusion swell occurs at the exit of the spinneret, resulting in a larger fiber fineness; and the processing temperature increases Will reduce the extrusion expansion ratio, thereby reducing the fiber fineness. This is because the polymer's own viscoelasticity affects the extrusion expansion ratio. The higher the temperature, the stronger the polymer molecular chain's ability to run, and the increased viscosity dissipation of the deformation energy stored in the melt during flow, resulting in elastic properties Weaken, so the extrusion expansion ratio decreases and the fiber fineness becomes smaller.
On the other hand, in the process of melt-blown spinning, the fibers in the molten state are gradually attenuated by the outside air, and the temperature is gradually attenuated, and increasing the temperature is beneficial to prolong the time of the fiber in the molten state, so that more fibers are drawn by high-speed hot air. Thus, the fiber fineness is reduced. Therefore, on the premise that the melt-blown raw materials are not excessively degraded, the temperature of each area such as the die head can be appropriately increased to make the fiber thinner, thereby improving the tensile breaking strength and filtration efficiency of the melt-blown product, but this also reduces the resistance; as the temperature When the temperature rises, the elongation at break of melt-blown products will decrease. When the temperature of each working area is too high, "flies" defects will be formed due to excessive fiber breakage.
D. Net bottom suction
The melt-blown fiber is drawn by high-speed hot air and laid on the receiver (net curtain) to form a fiber web. The remaining high-speed hot air needs to be smoothly absorbed under the receiver (net curtain), otherwise, the fiber cannot be fully absorbed into the screen On the screen, there will be defects such as "flying flowers", thin nets, and overturned nets if the net curtain is removed. In order to smoothly absorb the remaining high-speed hot air, it is necessary to install a net bottom suction device under the receiver (net curtain). The size of the suction at the bottom of the mesh is very important for the quality of the melt-blown fiber web, especially when producing a larger area density of melt-blown materials, increasing the suction at the bottom of the mesh will effectively improve the tensile strength and elongation of the product. Rate, the meltblown fiber web becomes denser from fluffy, the porosity becomes smaller, the filtration resistance decreases, and the filtration efficiency increases.
3. The following is a summary of the combined methods for improving the performance of meltblown cloth:
In the production of melt-blown products, the method of reducing the filtration resistance and improving the filtration efficiency is as follows: while the receiving distance is increased, the hot air speed or temperature is appropriately increased to reduce the suction at the bottom of the mesh, and the fiber fineness will change Small, the product is more fluffy. The methods that can improve both strength and elongation are as follows: when the spinning environment temperature is too high and the raw material melt index is too high, appropriately reduce the hot air flow or lower the temperature, reduce the receiving distance, and slightly increase the net bottom suction Or, when the spinning environment temperature is too low and the raw material melt index is too low, increase the hot air flow or increase the temperature, increase the receiving distance, and slightly reduce the bottom suction.
There are also relevant institutions that test the performance of the meltblown process parameters such as hot air temperature and pressure, receiving distance, etc. by testing the fiber fineness, mechanical properties, breathability, filtration efficiency, and hydrophilic properties of the meltblown nonwoven fabrics. The results show that: the fiber diameter increases with the increase of the temperature of the hot air, then decreases first and then increases; decreases with the increase of the pressure of the hot air. The strength increases with the increase of the pressure of the hot air, and decreases with the increase of the receiving distance The air permeability increases with the temperature of the hot air, the filtration efficiency increases with the pressure of the hot air, and the liquid absorption rate increases with the receiving distance.
4. Analysis of the causes of brittleness and hardness the next day after production of meltblown fabrics
Many customers may have encountered this problem: after the meltblown fabric was produced, it became brittle and hard overnight. At this time, should it be toughened with POE or softener?
Many manufacturers now cross the border from the plastic modification industry to the textile industry, and it is normal for production technology problems to appear "interlaced like mountains". how to solve this problem? This is closely related to production equipment, processes and raw materials, and cannot be generalized.
1. Uneven spinning and insufficient air flow from the cooler, resulting in uneven heat dissipation and internal stress, resulting in brittleness. It can be improved by adjusting the melt volume of the extruder, adjusting the temperature of the hot air fan, and increasing the air volume of the cold air fan.
2. From the perspective of raw materials, it may be that a low-melting grease spinneret is used, which is relatively thick. After 24 to 48 hours of complete crystallization, it will cause the meltblown fabric to become brittle and hard. The melt-blown 1500 meltblown material is thin, soft, and evenly distributed, and the meltblown fabric is soft.
3. It has a relationship with the raw materials and the processing temperature is too high. After the fiber is produced, there is a secondary crystallization rearrangement process inside the PP, which is actually seriously heated inside the screw, which has caused severe thermal degradation. If the initiator of the melt-blown peroxide process is not well controlled, such problems are prone to occur.
The most important thing in the peroxide process is how to complete the molecular chain break before the screw is extruded in time to prevent secondary residues from entering the non-woven screw to continue the reaction. This is a test of the screw equipment combination and formulation control.
4. The temperature of the melt-blown cloth just produced, especially for the cloth-spraying machine with large drums, may not have a fan, and the temperature of the melt-blown cloth is high after winding. Plastics have greater flexibility and toughness in high temperature environments and become brittle after cooling. It is the right way for manufacturers to produce according to the national standard "plastic polypropylene (PP) meltblown material".
The above analyzes the various possible causes that cause the brittle and hard second day after production of the meltblown cloth. Because the production equipment, process and raw materials of each factory are different, the manufacturer can only analyze and deal with it according to its own specific situation.
Fifth, let's talk about the seven common defects of melt-blown cloth:
1. Crystal point
Production mechanism:
a. The air velocity is too low or the melt viscosity is too high, and some melt filaments are not fully drawn;
b. When the viscosity of the melt is too small and the air speed is high, the holding effect of the spinneret on the melt is weakened, and the melt does not leave the spinneret before being drawn into fibers.
solutions:
a. Increase or decrease the temperature according to the melting index of the material;
b. Adjust the screw speed;
c. Choose the appropriate material for the melt head of the die head and spinneret.
2. Feixu
Production mechanism: The raw material and the corresponding spinning temperature are not well matched, which is caused by the higher temperature.
solutions:
a. If it is full-width fly batting, the screw spinning temperature and hot air temperature can be adjusted;
b. If it is a regional fly floc, the temperature of the die head in the corresponding location can be adjusted.
3. The cloth is brittle and hard
Production mechanism: The melt is not sprayed into fibers or multiple fibers stick together to cause brittle and hard melt-blown cloth.
solutions:
a. Adjust the hot air pressure;
b. Adjust the die head temperature;
c. Reduce the feeding amount;
d. Adjust the distance between the roller or curtain and the spinneret.
4. Plugging holes
Production mechanism: Generally, the plugging is mainly caused by excessive addition of electret masterbatch, many inorganic components, impurities in the melt-blown material and no filter screen.
solutions:
a. Reduce the amount of electret masterbatch;
b. Add filter net;
c. Use clean raw materials;
d. Replace the filter in time.
5. Uneven spinning
Production mechanism: The resistance of each spinneret hole or the size of the airflow is different, resulting in different spinneret amounts in each hole.
solutions:
a. Select precision die head and spinneret with the same pressure in each spinneret;
b. Replace the filter in time;
c. Regularly clean the spinneret;
d. Reduce the amount of electret masterbatch.
6. Stomata
Production mechanism: The moisture content of the material is too high, causing water vapor splashing during the spinning process and generating pores.
Solution: Dry the material.
7. Low filtration efficiency
Production mechanism:
a. The sprayed fiber is thick and the gap is large;
b. No electret masterbatch or insufficient addition;
c. No corona treatment or insufficient treatment.
solutions:
a. Increase the temperature;
b. Adjust the receiving distance of the cloth;
c. Reduce the feeding amount;
d. Increase air pressure;
f. Increase the content of electret masterbatch;
e. Electrostatic treatment.